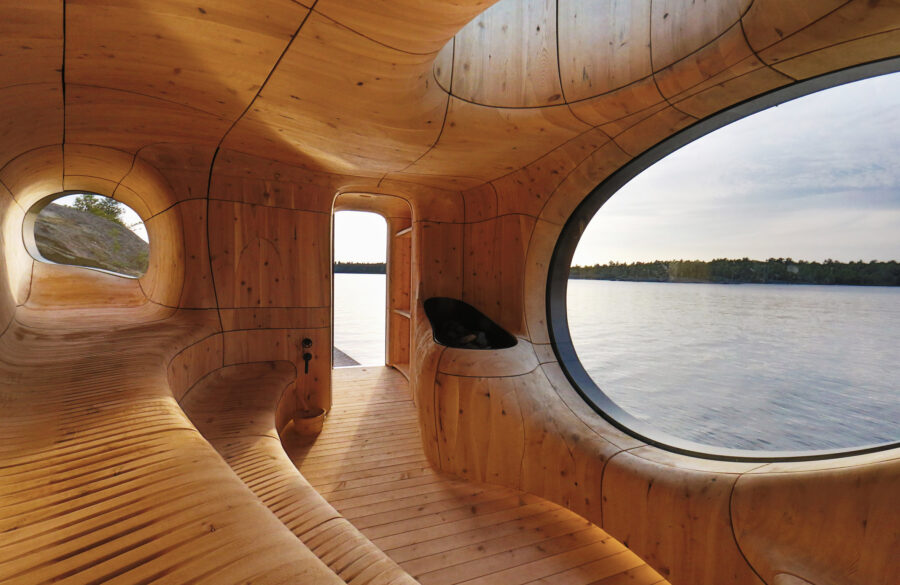
Striatus – 3D Concrete Printed Masonry Bridge from Zaha Hadid Architects on Vimeo.
3Dプリント×石積みのアーチ型橋〈Striatus〉は、チューリッヒ工科大学のブロックリサーチグループ(BRG)とザハ・ハディド・アーキテクツ コンピュテーション&デザイングループ(ZHACODE)によるプロジェクトです。インクリメンタル3D(in3D)と共同で、ホルシム(Holcim)社の協力のもと実施されました。
(以下、Zaha Hadid Architectsから提供されたテキストの抄訳)
©Naaro
〈Striatus〉は、3Dプリントされたコンクリートブロックをモルタルなしで組み立てた、アーチ型の無筋石積みの歩道橋です。
2021年11月までベネチアビエンナーレ期間中に展示されたこの16×12mの歩道橋は、熟練工の伝統技術と高度なコンピュテーショナルデザイン、エンジニアリング、ロボットマニュファクチャテクノロジーを組み合わせた初めての試みです。
〈Striatus〉という名称は、その構造論理と製作プロセスを反映しています。コンクリートブロックは主構造力と直交方向に積層プリントすることで、補強を必要としない圧縮のみのフニクラ構造を実現しています。
©Naaro
構造的な知識を持ち、ファブリケーションを意識し、エコロジーに責任を持ち、より少ないコストでより多くのものを建設するために的確に配置する、というコンクリートのための新しい言語を提案するため、〈Striatus〉は、石積み構造、3Dコンクリートプリント(3DCP)、現代デザインの関係を最適化し、従来のコンクリート建築に代わる選択肢を提示します。
©Naaro
〈Striatus〉は、幾何学的な構造によって強度を実現した無筋コンクリート構造物です。
圧縮時に最も性能を発揮する、人工石とも言えるコンクリート。そしてアーチ型の構造物は、材料を正確に配置することで、圧縮力のみで構成された状態となります。
これらを組み合わせることで、従来のコンクリート梁や床スラブのように、非効率的に材料を積み重ねるのではなく、形状によって強度を生み出すことができます。これは必要な材料の量を大幅に削減できるほか、より低強度で低公害の代替材料で建築できる可能性があります。
©Naaro
ブロックが水平方向に動こうとする力は、引張力をかけるスチール製のタイロッドが吸収します。また、乾式で設置されたブロック間にかかる応力集中を避けるため、境界面の摩擦特性をコントロールするネオプレンのパッドを配置しています。
これらは、歴史的な石造建築における鉛シートやモルタルと同様の効果を示します。
©Naaro
印刷層を主構造力に対し直交するよう積層することで、圧縮された状態で保持され、印刷層間の剥離を回避することができます。
また、アディティブ・マニュファクチャリング(積層造形)により、コンクリート梁のように立体的にコンクリートを充填しない中空断面が可能となり、必要な材料量を削減することができます。
©In3D
鉄筋やバインダーを使わない乾式工法でつくられた〈Striatus〉は、設置、解体、再組み立て、再利用を繰り返すことができ、サステナビリティの3R(リデュース、リユース、リサイクル)がコンクリート構造物に適用できることを示しています。この循環型設計により、〈Striatus〉はフットプリントを大幅に削減します。
©Naaro
リデュース:構造的なジオメトリとアディティブ・マニュファクチャリングにより、資源の消費を最小限に抑え、建設廃棄物を削減しています。これはコンクリート使用量の削減のみではありません。コンクリート中に鉄筋を埋め込むのに比べ、外付けの結束バンドでアーチ形状の推力を吸収することで、必要な鉄の量を劇的に減らすことができます。鉄筋は炭素濃度が高い素材であり、単位質量で比べると標準的なコンクリートの10倍以上になります。
©Naaro
リユース:循環型社会の実現と長寿命化を図ります。〈Striatus〉はバインダーや接着剤を一切使用しない乾式組立のため、橋を解体して別の場所で再利用できる設計になっています。また、フニクラ構造により、使用中も応力が小さく抑えられ、構造的な強度が損なわれることはありません。
©Naaro
リサイクル:異なる材料同士を容易に分離できることで、〈Striatus〉の各コンポーネントは、最小限のエネルギーとコストで簡単にリサイクルすることができます。また、3Dプリントは、使い捨ての型枠のような廃棄物とそのコストを回避することができます。
©Naaro
〈Striatus〉は、一般的な水平レイヤーの3Dプリントとは異なり、6軸ロボットアームを使用することでより自由度高く、かつ正確にプリントすることができます。この新世代の3DCPとアーチ型石積みの設計を組み合わせることで、鉄筋や補強なしでの構造を可能にしています。
©In3D
©In3D
3DCP×石工のデザインとすることで、製造業や建設業に熟練した労働力を再導入することが可能になります。
製造のデジタル化と熟練した組立・建設技術のデジタル拡張により、歴史的に蓄積された知識に若い世代がアクセスできるようになり、コンピュータやロボット技術を使用して工業化建設に向けて体系的にアップグレードすることが可能になります。
©In3D
オートメーションと組立ライン生産に偏った、強引で物質的に無駄の多い経済とは対照的に、3DCPの石工は、人間と機械の共生する経済の可能性を示しています。これは、環境的にも、社会文化的にも、そして経済的にも持続可能な20世紀型経済の代替案となるものです。
©In3D
©In3D
デザイン、エンジニアリング、ファブリケーション、コンストラクションを統合した〈Striatus〉は、従来の学際的な関係を再定義します。
Photograph by Tom Van Mele
ブロックの精密な製造は、このプロセスに関与するさまざまな分野に特化した一連のソフトウェアツール間の明確なデータ交換によって可能となりました。この共同開発のアプローチは、AEC(建築・土木・建設)産業におけるコラボレーションと研究のためのオープンソースのコンピュテーショナルフレームワークである「COMPAS」を使用しています。
この「COMPAS」により、非常に厳しいスケジュールと予算であり、移動が不可能な時期において、5カ国にわたるプロジェクトのキープレイヤー間の円滑なコミュニケーションが可能となりました。
Photograph by Tom Van Mele
〈Striatus〉は、より少ないものでより多くのものをつくるための青写真を提示しています。
ブロックリサーチグループがホルシム社と共同で開発した「アーチ型リブ補強無筋コンクリート床」と同じ構造原理とアプローチでつくられた〈Striatus〉は、従来の非効率な床スラブの代替案を提案します。
Photograph by Tom Van Mele
この新しい床システムは、一般的な鉄筋コンクリートの床スラブと比較して、コンクリートは30%、鉄骨は10%で構成されています。
また、フニクラ構造は応力が非常に小さく強度を損なわないため、建設廃材のリサイクル率を高めることが可能になっています。この床システムはプレハブかつ乾式組み立てのため、解体や再利用が可能で、使用後は簡単かつきれいにリサイクルすることができます。
Photograph by Alessandro Dell’Endice
今後30年間に世界中で建設される床面積は3000億m²と推定され、ほとんどの高層ビル(10階以上)では床が重量の40%以上を占めています。〈Striatus〉が示した原則を導入することで、私たちの時代の決定的な課題に対処するために、建築環境の設計と建設の方法を変革することができます。
Photograph by Alessandro Dell’Endice
Photograph by Alessandro Dell’Endice
Photograph by Tom Van Mele
Photograph by Tom Van Mele
Plan
Elevation A
Elevation B
Elevation C
Section A
Section B
以下、Zaha Hadid Architectsのリリース(英文)です。
Striatus
An arched 3D-concrete-printed masonry bridge
A project by the Block Research Group (BRG) at ETH Zurich and
Zaha Hadid Architects Computation and Design Group (ZHACODE),
in collaboration with incremental3D (in3D), made possible by HolcimPress release
Striatus is an arched, unreinforced masonry footbridge composed of 3D-printed concrete blocks assembled without mortar. Exhibited at the Giardini della Marinaressa during the Venice Architecture Biennale until November 2021, the 16×12-metre footbridge is the first of its kind, combining traditional techniques of master builders with advanced computational design, engineering and robotic manufacturing technologies.
The name “Striatus” reflects its structural logic and fabrication process. Concrete is printed in layers orthogonal to the main structural forces to create a “striated” compression-only funicular structure that requires no reinforcement.
A new language for concrete
Proposing a new language for concrete that is structurally informed, fabrication aware, ecologically responsible and precisely placed to build more with less, Striatus optimises the interrelated properties of masonry structures, 3D concrete printing (3DCP) and contemporary design; presenting an alternative to traditional concrete construction.
Strength through geometry
Striatus is an unreinforced concrete structure that achieves strength through geometry. Concrete can be considered an artificial stone that performs best in compression. In arched and vaulted structures, material can be placed precisely so that forces can travel to the supports in pure compression. Strength is created through geometry, rather than an inefficient accumulation of materials as in conventional concrete beams and flat floor slabs. This presents opportunities to significantly reduce the amount of material needed to span space as well as the possibility to build with lower-strength, less-polluting alternatives.
Striatus’ bifurcating deck geometry responds to its site conditions. The funicular shape of its structural arches has been defined by limit analysis techniques and equilibrium methods, such as thrust network analysis, originally developed for the structural assessment of historic masonry vaults; its crescent profile encompasses the thrust lines that trace compressive forces through the structure for all loading cases.
Steel tension ties absorb the horizontal thrust of the arches. Neoprene pads placed in between the dry-assembled blocks avoid stress concentrations and control the friction properties of the interfaces, echoing the use of lead sheets or soft mortar in historical masonry construction.
In plan, the boundaries of the structure form deep arches that transfer horizontal loads (for example, from visitors leaning against the balustrades) to the supports in pure compression. Advanced discrete element modelling (DEM) was used to refine and optimise the blocks’ stereotomy and to check the stability of the entire assembly under extreme loading cases or differential settlements of the supports.
The bridge’s 53 3DCP voussoirs have been produced using non-parallel print layers that are orthogonal to the dominant flow of forces. This avoids delamination between the print layers as they are held together in compression. The additive manufacturing process ensures the structural depth of the components can be achieved without producing blocks with a solid section, hence reducing the amount of material needed compared to subtractive fabrication methods or casting.
Striatus follows masonry structural logic on two levels. As a whole, the bridge behaves as a series of leaning unreinforced voussoir arches, with discretisations orthogonal to the dominant flow of compressive forces, following the same structural principles as arched Roman bridges in stone. Locally, on the level of the voussoir, the 3DCP layers behave as traditional brick masonry evident in the inclined rows of bricks within Nubian or Mexican vaulting.
Sustainable digital concrete
Circular by design, Striatus places material only where needed, significantly reducing its environmental footprint. Built without reinforcement and using dry assembly without binders, Striatus can be installed, dismantled, reassembled and repurposed repeatedly; demonstrating how the three R’s of sustainability (Reduce, Reuse, Recycle) can be applied to concrete structures.
Reduce: Lowering embodied emissions through structural geometry and additive manufacturing that minimises the consumption of resources and eliminates construction waste.
Placing concrete only there where needed, 3DCP minimises the amount of material required, while the low-stress, compression-only funicular geometry of Striatus proposes the further development of 3DCP that will enable the use of much lower-strength, less-polluting printable materials.
Compared to embedded reinforcement in concrete, Striatus uses external ties to absorb the thrust of its arched shape and dramatically reduce the amount of steel required. A high carbon-intense material, steel reinforcement (100% recycled) per unit mass is more than ten times that of standard concrete.
Reuse: Improving circularity and longevity. Unlike conventional reinforced concrete structures, Striatus is designed to be dry assembled without any binder or glue, enabling the bridge to be dismantled and reused in other locations. Its funicular design ensures the 3DCP blocks experience low stresses throughout their use, resulting in no loss of structural integrity. Striatus separates components in compression and tension, ensuring external ties can be easily accessed and maintained, resulting in a longer lifespan for the entire structure.
Recycle: By ensuring different materials are separated and separable, each component of Striatus can easily be recycled with minimal energy and cost. 3D printing also avoids the waste and costs associated with single-use moulds. Additionally, the component materials within Striatus remain separate and separable with the use of mechanical connections such as simple dry contacts between the voussoirs rather than chemical glues or binders, ensuring a simple, low-energy recycling process at the end of the elements’ life, potentially after multiple cycles of reuse.
Robotic 3D concrete printing
Unlike typical extrusion 3D printing in simple horizontal layers, Striatus uses a two-component (2K) concrete ink with corresponding printing head and pumping arrangement to precisely print non-uniform and non-parallel layers via a 6-axis, multi-DOF robotic arm. This new generation of 3D concrete printing in combination with the arched masonry design allows the resulting components to be used structurally without any reinforcement or post-tensioning.
To prevent misalignment between the direction of structural forces and the orientation of material layers that arises from typical shape-agnostic slicing of explicitly modelled geometry, a custom-developed design pipeline was formulated for Striatus to ensure that its printed layers are wholly aligned with the direction of compression forces throughout the entire bridge and also locally through each 3D-printed block. To address issues and challenges that could prevent in-between stability during printing, the coherence and feasibility of the gradually evolving print paths have been modelled using a Functional Representation (FRep) process.
This process encodes and continuously checks rules of minimum overlap, maximum cantilever between print layers and print length, print speed and the volume of wet concrete extruded. These measures, typically used in horizontally layered 3DCP, have been advanced and refined to work on an inclined-plane setting:
- The angular differences between start and end planes of all 53 printed blocks have been simultaneously adjusted to meet multiple criteria such as an appropriate structural contact and angle between adjacent blocks, and maximum print inclination.
- The careful design and iterative refinement of the hollow cross-sections and infill triangulation have ensured that material is placed corresponding to the precisely analysed, local structural performance of each block. This design and optimisation have been applied to each individual layer of every block (with 500 print layers on average per block), ensuring that all blocks are as hollow and light as possible, and consequently use the least amount of material possible while maintaining structural integrity under all loading conditions.
- The resulting intricate cross-sectional design has been processed into a single, continuous print path meeting various criteria that include appropriate print speed and turning radii, structurally required material width and thickness, and controlled expression of naturally occurring printing artefacts.
A nuanced aspect of robotic 3DCP masonry is the re-introduction of intelligence and highly skilled labour into the manufacturing and construction industry. The digitisation of fabrication and digital augmentation of skilled assembly and construction techniques makes historically-accrued knowledge accessible to younger generations and enables its systematic upgrade towards industrialised construction through the use of computational and robotic technologies. In stark contrast to a brute force, and often materially wasteful economy biased towards automation and assembly line production, 3DCP masonry introduces possibilities of a symbiotic human-machine economy. This promises an environmentally, socio-culturally and economically sustainable alternative to its 20th-century predecessor.
Computational design-to-construction integration
Integrating design, engineering, fabrication and construction, Striatus redefines conventional interdisciplinary relations. The precise manufacturing of the blocks was enabled by well-defined data exchange between the various domain-specific software toolchains involved in the process. This co-development approach was facilitated through the use of COMPAS, an open-source computational framework for collaboration and research in the AEC industry, which enabled the fluent interaction among the key players of the project, working together in five different countries, under a very tight schedule and budget, at a time in which travelling was not possible.
Disruptive outlook
Striatus offers a blueprint for building more with less. Created with the same structural principles and a similar fully-integrated computational design-to-fabrication approach that form the basis of the vaulted, rib-stiffened, unreinforced concrete floors being developed by the Block Research Group in partnership with Holcim, Striatus proposes an alternative to the standard inefficient floor slabs within any building.
Compared to typical reinforced concrete flat floor slabs, this new floor system uses only 30% of the volume of concrete and just 10% of the amount of steel. The very low stresses within the funicular structure also enable the use of low-embodied-carbon concrete that incorporates high percentages of recycled construction waste. Prefabricated and dry-assembled, and therefore fully demountable and reusable, this floor system is easily and cleanly recyclable at end-of-life.
With an estimated 300 billion square metres of floor area to be constructed worldwide over the next 30 years, and floors comprising more than 40% of the weight of most high-rise buildings (10+ storeys), introducing the principles demonstrated by Striatus would truly disrupt the construction industry — transforming how we design and construct our built environment to address the defining challenges of our era.
Fact sheet
Overall
Maximum height = 3.5 m
Minimum head height = 2.2 m
Total surface area = 216 m²
Total covered area = 50 m²
Longest span = 15.10 m
Shortest span = 4.95 m
Material density of 3D-printed concrete = ~2350 kg/m³
Total mass of the structure
3DCP blocks = 24.5 ton
footings, tension ties = 5.2 tonVoussoirs / Blocks
Number of voussoirs = 53
Thicknesses of voussoirs = 0.05m – 0.35 m
Volume (solid) of voussoirs = 19.18 m³
3D-printed concrete
3D-printing path lengths (per block) = 602 m – 1754 m
3D-printing total path length (all blocks) = 58 km
3D-printing total print time (all blocks) = 84 hours
(incl. pre-print and post-print procedures)
3D-printing layer heights = 4.46 mm – 11.98 mm
3D-printed mass per block = 217 kg – 783 kg
3D-printing widths
Deck Blocks = 25 mm – 50 mm
Balustrade Blocks = 40 mmLocation
Giardino della Marinaressa, Venice, Italy
45°25’53.6″N 12°21’09.8″EProject Partners
Block Research Group (BRG) at ETH Zurich
Established in 2009, the Block Research Group (BRG) at the Institute of Technology in Architecture at ETH Zurich is led by Prof. Dr. Philippe Block and Dr. Tom Van Mele. Research at the BRG focuses on the assessment of historic masonry structures, computational form-finding and structural design, and innovative construction technologies. Learning from the master builders of the past, the BRG develops novel design and engineering approaches for highly efficient and expressive structural form and proposes new and economical construction approaches. To address the grand challenges posed by climate change, the group’s research and built prototypes strive the motto “strength through geometry” to reduce embodied greenhouse gas emissions and utilise fewer first-use resources. To minimise construction waste and increase labour productivity, the group develops innovative bespoke prefabrication strategies and novel construction paradigms that employ digital fabrication. The BRG shares its new algorithms and computational tools for structurally informed design through the open-source computational framework COMPAS. https://block.arch.ethz.chZaha Hadid Architects Computation and Design Group (ZHACODE)
Founded in 2007 by Patrik Schumacher, Nils Fischer and Shajay Bhooshan, the Zaha Hadid Architects Computation and Design (ZHACODE) group is a practice-embedded research team focussing on computational geometry and strategic innovations that bridge from disciplinary advances to project-based applications. We explore novel spatial and experiential affordances of new technologies in structure and fabrication-aware geometry creation, robotic fabrication and industrialised construction. We also incorporate these advances into workflows at ZHA to address pressing issues of participatory and sustainable development of the built environment. Our ever-increasing design and project contributions at ZHA are powered by a bespoke computational framework. This framework continues to accrue collaborative and field-tested research spanning computer graphics, digital design, maturing robotic construction technologies, and participatory, end-user-oriented technologies of game engines and web services. Together, our ethos, projects and technologies aim to create an architecture suited for the 21st century – interaction dense, experience-rich, user-focussed and resource-effective.
http://www.zaha-hadid.comincremental3D
Founded in 2017, incremental3d GmbH specializes in the production of individual and complex objects utilizing 3d concrete printing (3DCP). The founding and management team consists of the architects Georg Grasser, Lukas Härtenberger and Johannes Megens. Through years of joint research at the University of Innsbruck, they developed digital tools, processes and experience for 3DCP that allowed them to take their knowledge to the market. The team combines creativity and technology to produce high-quality concrete objects that push the limits of concrete design. incremental3d collaborated on a number of furniture design commissions and is currently approaching applications in architecture and construction. They are constantly updating processes and tools in order to improve and explore the design potential in additive manufacturing of concrete. A new addition is selective colouring with 3DCP, which allows to dye concrete in various colours and intensities (supported by AWS).
https://www.incremental3d.euHolcim
Holcim builds progress for people and the planet. As a global leader in innovative and sustainable building solutions, Holcim is enabling greener cities, smarter infrastructure and improving living standards around the world. With sustainability at the core of its strategy, Holcim is becoming a net-zero company, with its people and communities at the heart of its success. The company is driving the circular economy as a world leader in recycling to build more with less. Holcim is the company behind some of the world’s most trusted brands in the building sector including ACC, Aggregate Industries, Ambuja Cement, Disensa, Firestone Building Products, Geocycle, Holcim and Lafarge. Holcim is 70,000 people passionate about building progress for people and the planet across its 70 markets and four business segments: Cement, Ready-Mix Concrete, Aggregates and Solutions & Products.
https://www.holcim.comFull credits
Design
ZHACODE: Jianfei Chu, Vishu Bhooshan, Henry David Louth, Shajay Bhooshan, Patrik Schumacher
ETH BRG: Tom Van Mele, Alessandro Dell’Endice, Philippe BlockStructural engineering
ETH BRG: Tom Van Mele, Alessandro Dell’Endice, Sam Bouten, Philippe BlockFabrication design
ETH BRG: Shajay Bhooshan, Alessandro Dell’Endice, Sam Bouten, Chaoyu Du, Tom Van Mele
ZHACODE: Vishu Bhooshan, Philip Singer, Tommaso Casucci3D concrete printing
In3D: Johannes Megens, Georg Grasser, Sandro Sanin, Nikolas Janitsch, Janos MohacsiConcrete material development
Holcim: Christian Blachier, Marjorie Chantin-Coquard, Helene Lombois-Burger, Francis Steiner
LafargeHolcim Spain: Benito Carrion, Jose Manuel ArnauAssembly & Construction
Bürgin Creations: Theo Bürgin, Semir Mächler, Calvin Graf
ETH BRG: Alessandro Dell’Endice, Tom Van MeleLogistics
ETH BRG: Alessandro Dell’Endice, Tom Van Mele
Holcim Switzerland & Italy: Michele Alverdi
LafargeHolcim Spain: Ricardo de Pablos, José Luis RomeroAdditional partners
Ackermann GmbH [CNC timber formwork]
L2F Architettura [site measurements]
Pletscher [steel supports]
ZB Laser [lasercutting neoprene]Documentation
ZHACODE: Jianfei Chu, Cesar Fragachan, Vishu Bhooshan, Philip Singer, Edward Meyers, Shajay Bhooshan
ETH BRG: Tom Van Mele, Alessandro Dell’Endice, Philippe Block
In3D: Alexander Gugitscher, Sandro Sanin, Nikolas Janitsch
naaro
LBS Fotografia
「Striatus 3D Printed Concrete Bridge」Zaha Hadid Architects公式サイト
https://www.zaha-hadid.com/design/striatus/